Interview by job type
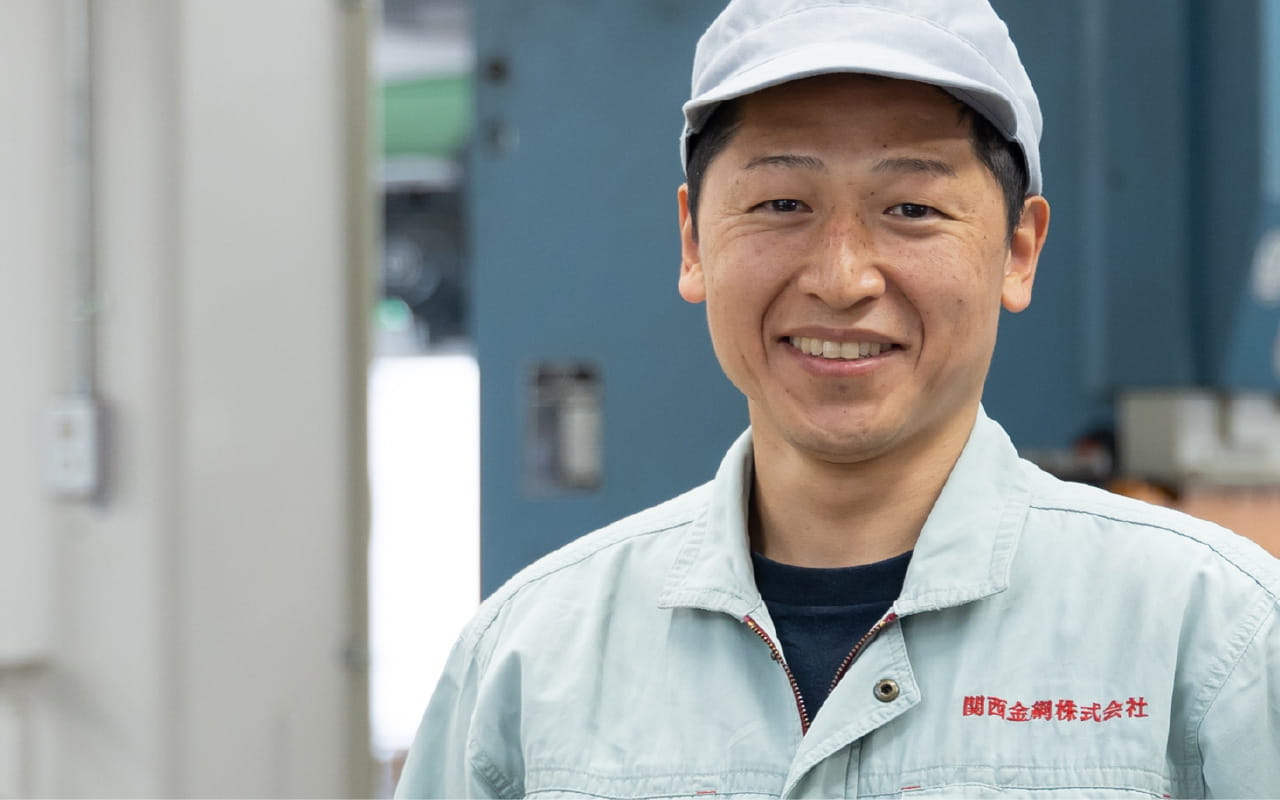
Learn and learn various manufacturing methods.
The goal is to have a relationship that can help each other.
- #4th to 6th year
- #Manufacturers
- #Graduated from the Faculty of Humanities
- #Domestic
It is essential to think carefully about what to do and proceed well.
I am mainly in charge of the production of stainless steel filters and vibration sieves using wire mesh. Most products are completed by combining a frame made by cutting, pressing, welding, etc. with a wire mesh according to the customer's request, but since the specifications differ depending on the customer's request, some are completed in one day, while others take about one month. Therefore, it is essential to think carefully about what to do on the day so that the delivery date is not delayed, and to proceed with the work well. In addition to manufacturing, we perform all work, including inspection and packaging, but at first we could only assist seniors and proceed according to instructions. However, recently, I have been entrusted with a lot of work, and I have realized that I am growing steadily.
Kansai wire mesh products are very diverse, and even in the same department, others are making products using a completely different manufacturing method. When my work is busy, the people around me will help me, so when I am busy, my goal is to learn other manufacturing methods and help each other so that I can help. We will continue to strive to create better products while gaining more experience and making decisions on our own without consulting our seniors and thinking about how to do it.
A day schedule
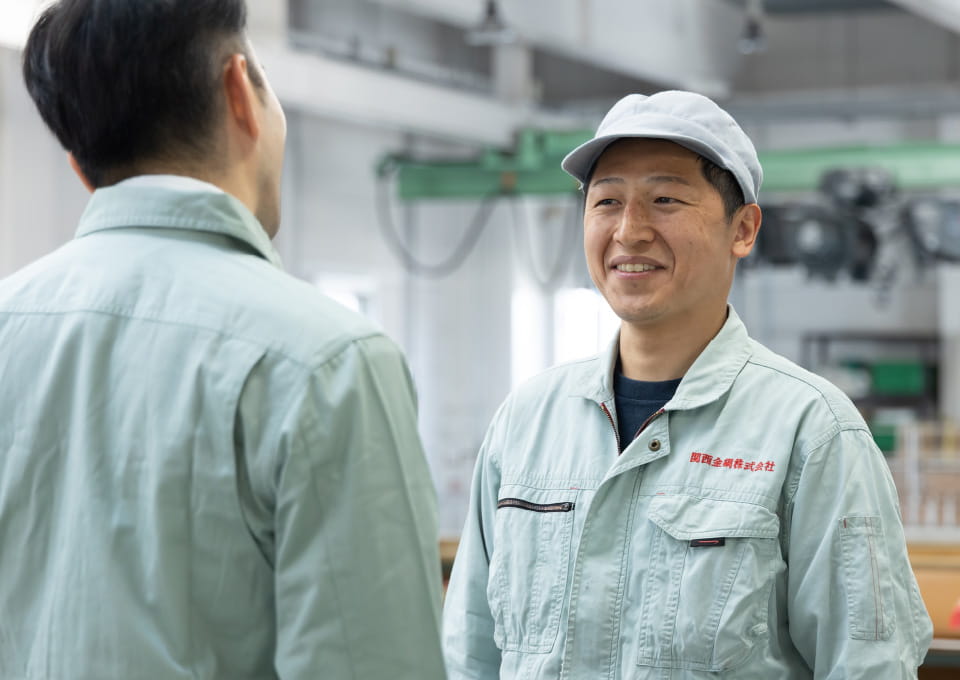
- 8:30
- Start-up
Radio exercises, morning meetings, communication of loading large luggage, and
If you need human resources, ask for support.
- 9:00
- Start of production
Use rolls to bend the frame material according to the specifications, and welding and polishing work.
- 12:00
- Lunch
- 13:00
- Resuming work
Weld the net to the finished frame and finish polishing.
- 15:00
- Cleaning and packing
Wash with detergent, confirm that there are no scratches or dirt, and wrap it to complete.
- 17:25
- End of work
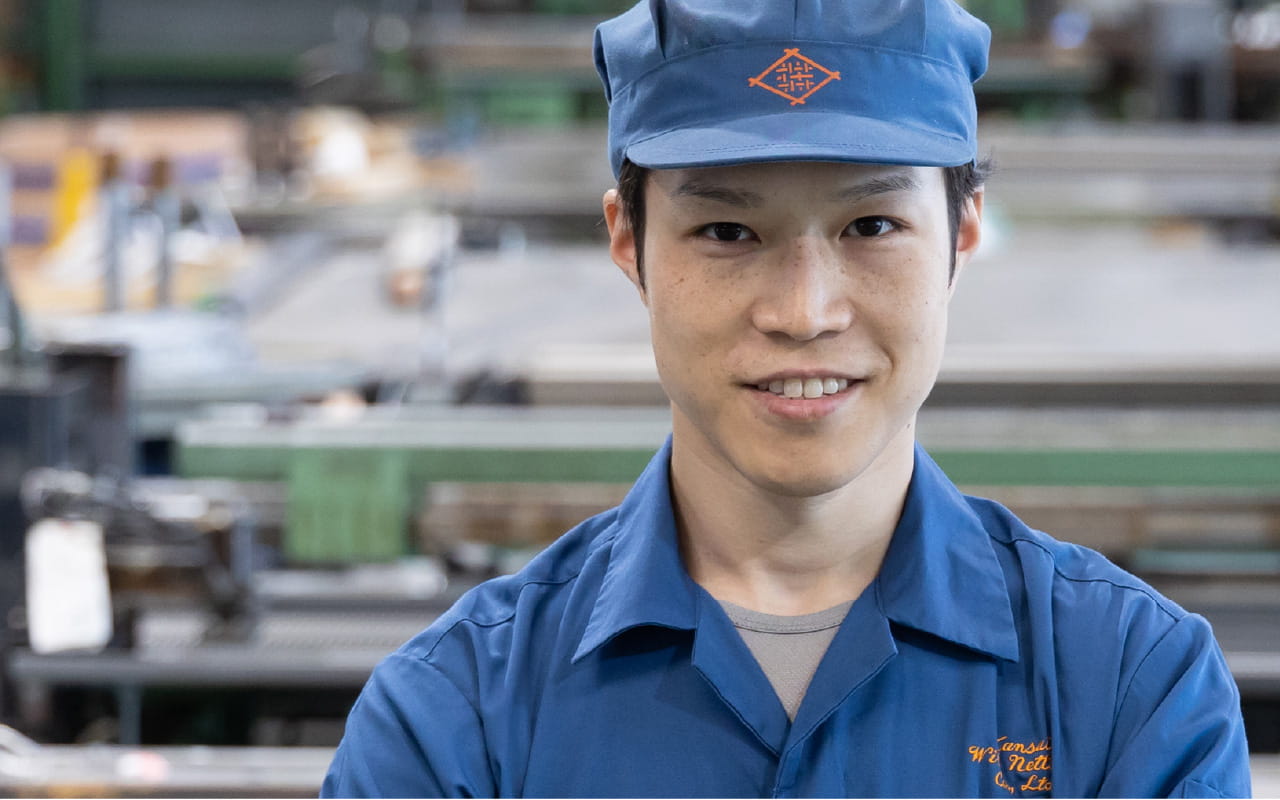
In addition to manufacturing work, if there is a chance
I want to take on the challenge regardless of my job.
- #4th to 6th year
- #Manufacturers
- #Domestic
By accumulating experience and product knowledge, we aim to play an active role in a wider range of situations.
The main tasks of the Conveyor finishing group at the Osaka Plant to which I belong, are to be finished as a product by measuring the length of the conveyor belts and welding the belts of the previous Conveyor Manufacturing Group. Before joining the company, I would like to work related to manufacturing and processing, and I feel rewarding to be involved in the actual work. In addition, I think every day about how I can improve work efficiency, reduce mistakes, and improve product quality, and execute it every day. It is also a great rewarding job that makes me feel the joy of my own growth and work when I realize it.
The Osaka Plant manufactures a wide variety of conveyor belts, just like wire mesh, and by experiencing manufacturing processes other than finishing and acquiring product knowledge such as specifications and conditions, I want to use my power in a wider range of situations. In addition to manufacturing work, I am also interested in work outside the Osaka Plant and clerical work, so if I have a chance, I would like to literally take on the challenge without choosing any work.
A day schedule
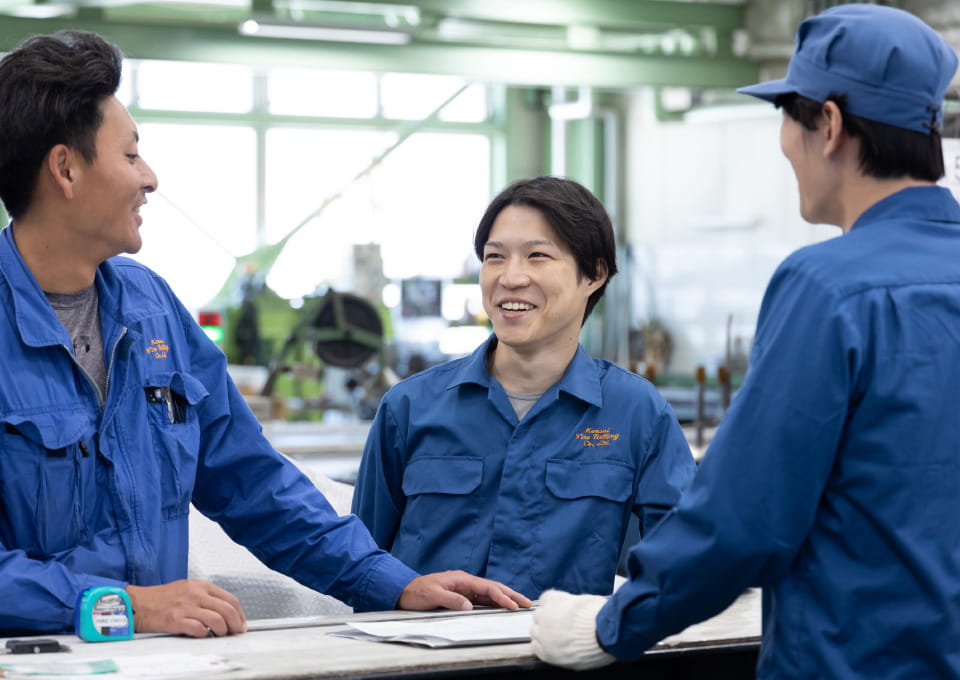
- 8:25
- Start-up, meeting
We will report on the rough schedule of one week and the contents of the previous week's meeting.
- 8:50
- Equipment inspection
Inspect the equipment to be used before use and check in advance whether it works properly without any problems or failures.
- 9:00
- Finishing work, welding
The length required for the product is measured, the edges are trimmed, and then welded.
- 12:00
- Lunch
- 13:00
- Finishing work, cleaning
Use acid to remove the burnt on the edges that have been scorched and blackened by welding. After that, the final degreasing cleaning is performed.
- 16:50
- Office work
Enter the man-hours of the completed work into the management system.
- 17:05
- Cleaning
The day is completed by cleaning and organizing tools so that the start of the next day can be done without waste.
- 17:15
- End of work
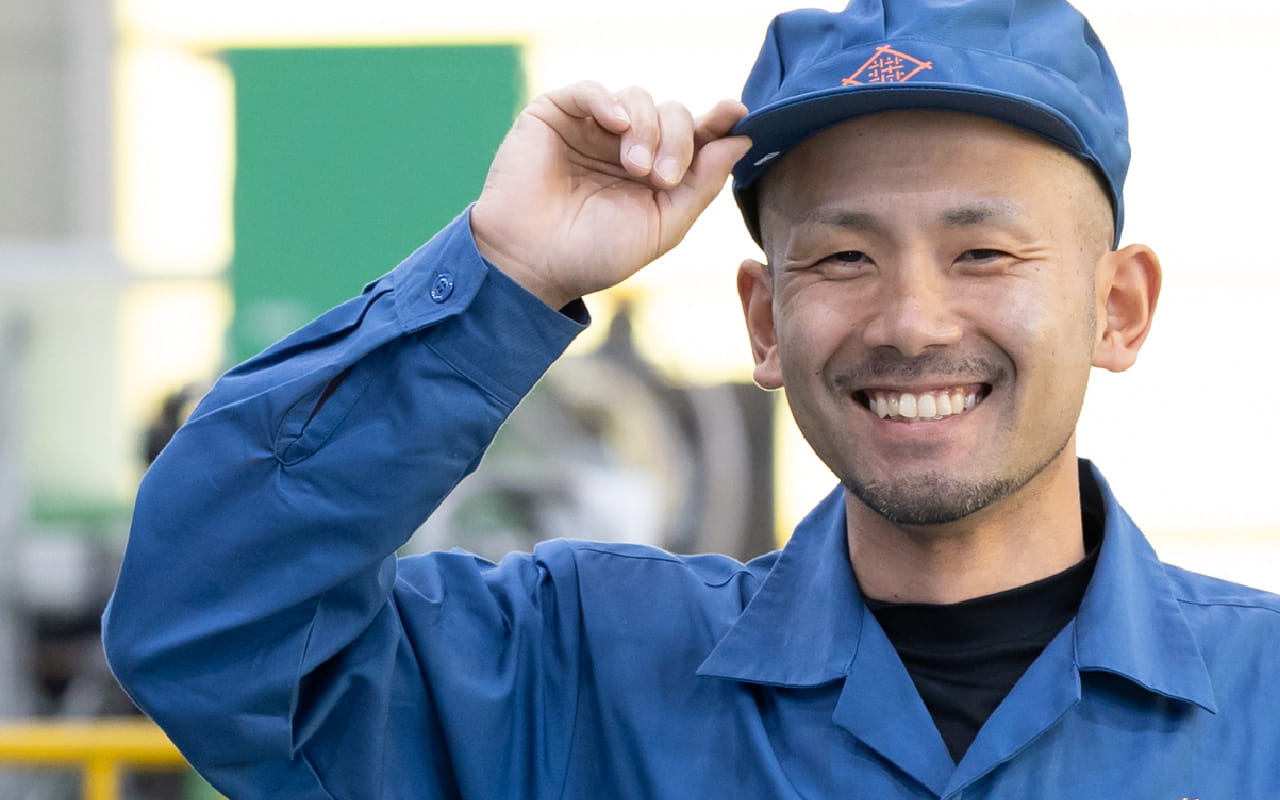
The high technology and knowledge of Kansai wire network
Our mission is to pass it on to the next generation.
- #7th to 9th year
- #Manufacturers
- #Graduated from the Faculty of Humanities
- #Domestic
Growth and achievement that can be felt when a satisfactory product is completed.
Most of Kansai wire mesh products are custom-made products made to solve customers' problems, and the crimp (wire mesh) manufacturing group at the Osaka Plant of the manufacturing department to which I belong, also produces a wide variety of wire mesh according to customer specifications and requests. There are also various materials, wire diameters, and shapes used for wire mesh production, and they need to be used properly according to specifications. In addition, since most of the wire mesh is used as vibrating sieves, the vertical and horizontal lines are firmly engaged and the daily work is focused on protecting the quality that can be used for many years. I am facing it. Compared to seniors who have created the high quality of the Kansai wire mesh so far, they always ask themselves what the products they have worked on and whether they have been satisfied with the customer hill, and when the product that can be satisfied is completed, It is a job where you can feel your own growth and feel a sense of accomplishment.
On the other hand, there are many types of wire mesh that we have not yet been involved in manufacturing because we manufacture multi-products, so we can experience them first and eventually complete all kinds of wire mesh on our own. At present, we mainly use wire mesh fabrication, but we also want to deepen our knowledge of wire mesh manufacturing in general and improve the productivity of the entire factory by considering what kind of work the Klimp Finishing Group, which is our later process, is doing and whether there are any points that can be improved. In addition, we will firmly fulfill the role of passing on the high technology and knowledge of wire mesh manufacturing that Kansai wire mesh has cultivated to the next young juniors.
A day schedule
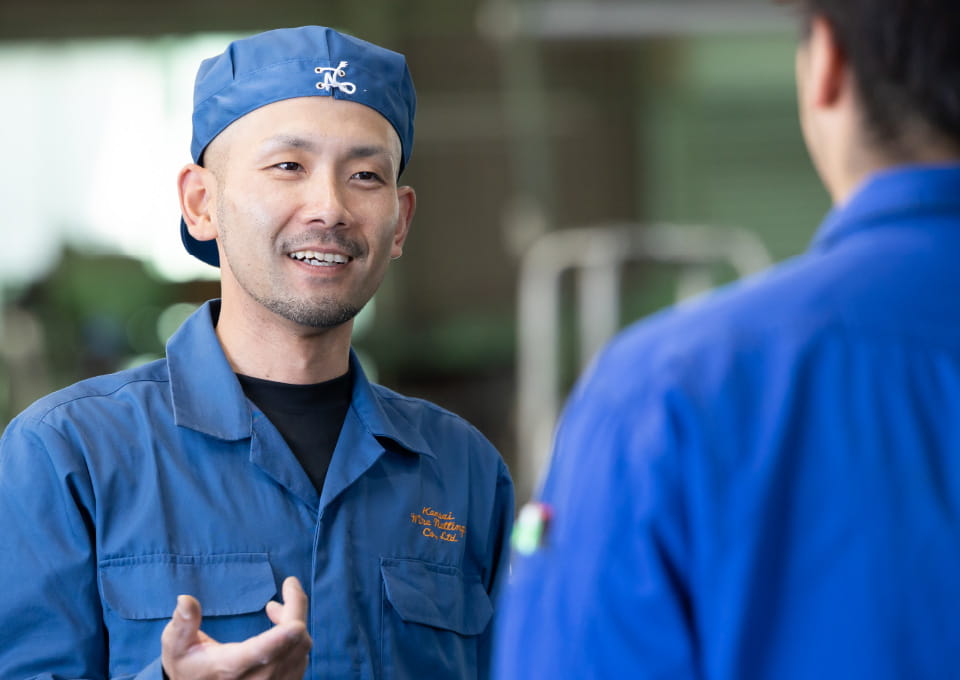
- 8:25
- Start-up, equipment inspection
Inspection of equipment to be used on the day.
- 8:35
- On-site meeting
Status reports up to the previous day, work content reports on the day, and sharing other communication items.
- 8:45
- Preparation of wire mesh weaving
Confirmation of production slip (confirmation of customer requirements), preparation of deployment drawing, preparation of wire materials, preparation of molds (gears)
- 9:15
- Wire mesh fabric
Process the vertical line with a crimp machine and set the vertical line on the loom.
- 12:00
- Lunch break
- 12:45
- Wire mesh fabric
Beginning wire mesh weaving with a loom (weave a horizontal line in a vertical line)
- 15:00
- Break
- 15:05
- In-process inspection
Intermediate inspection conducted before finishing work after completion of weaving (conducted by qualified persons other than weaving workers)
- 15:15
- Wire mesh finishing work
Cut the wire mesh after weaving and hook processing
- 16:45
- In-process inspection
Intermediate inspection (conducted by qualified persons other than the finishing worker) after completion of the manufacturing process ・ Passing slips and products to the final process inspection group.
- 17:05
- 5S Activities
Clean the workplace on the day and lock the doors (check sheet when leaving the company)
- 17:15
- End of work
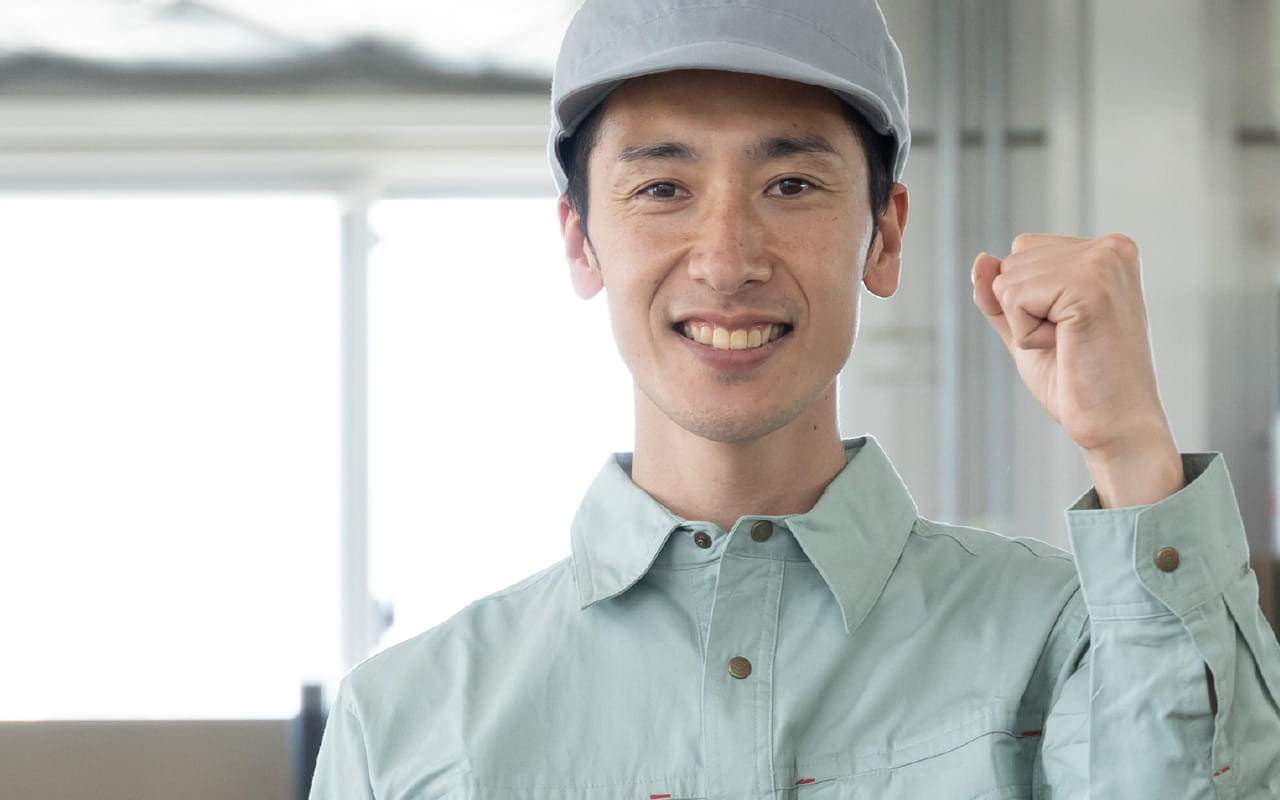
The joy and pride of products that are active as "powers under the edges".
- #7th to 9th year
- #Manufacturers
- #Graduated from the Faculty of Science
- #Domestic
We create products from scratch with our own hands.
You can enjoy the real pleasure of manufacturing.
I am currently in charge of the process of joining wire mesh and frame at the Amagasaki Plant of the Manufacturing Department to manufacture sieves. Place the wire mesh on the frame and connect the wire mesh with a solder while pulling it, but you can enjoy the real pleasure of manufacturing that creates products from scratch with your own hands and the sense of accomplishment and fulfillment at the time of completion It is a very rewarding job that you can enjoy. Also, I don't see the products produced by my hands in everyday life, but when I think that it is indispensable in every manufacturing site, and that it supports our lives as a "power under the edge", I often feel happy and proud.
Since I was transferred from the product center at the head office, I often feel that I am short of experience, but with the support of people around me, I want to gain more experience and acquire skills, and become a little quicker to what I need for the company. First of all, I would like to make my sieve manufacturing skills I am currently in charge of, and in the future, I would like to take on the challenge of processing techniques such as welding and expand my range of practical work.
A day schedule
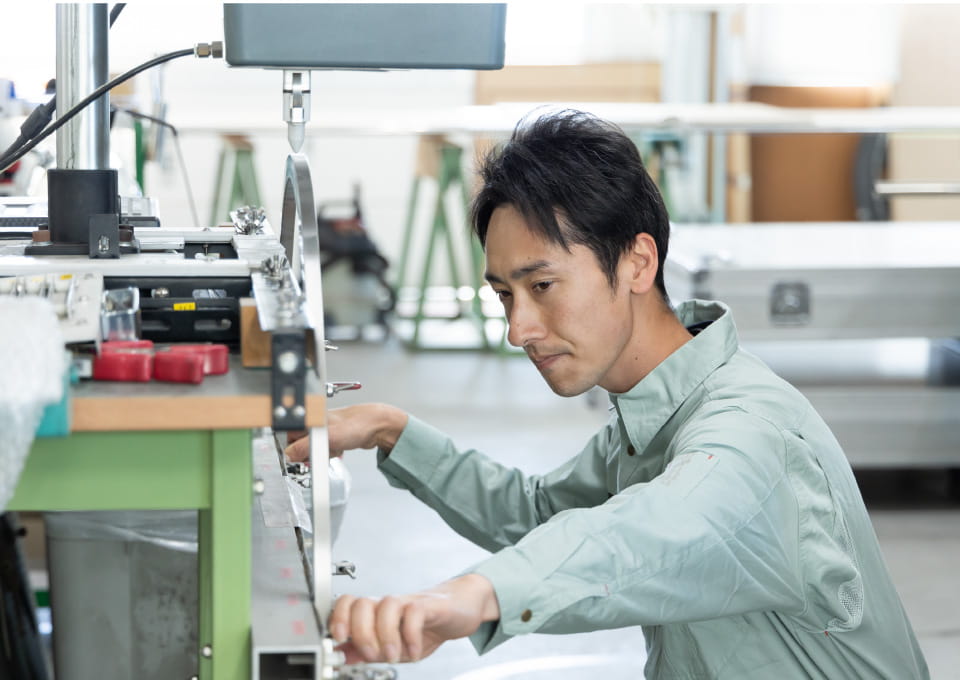
- 8:30
- Beginning, radio exercises
- 9:00
- Net wash
Since there is oil stains on the net, wash it with a brush using wire material.
The frame grinding is also performed in this process.
- 11:00
- A solder
Place the net on the frame and attach a flux (painting agent).
Do the soldering while pulling it.
- 12:00
- Lunch break
- 12:45
- Resuming operations
- 15:00
- Break
- 16:00
- Washing
Wash off the flux (painting agent) remaining in the wire mesh.
- 17:15
- End of work