
Case Studies
2023.05.10 up
Reduce gas fuel costs for continuous heat treatment furnaces by reducing the weight of belts
We reviewed the specifications of wire conveyor belts used for heat treatment of metal parts. We reduced the weight of the belt and led to a reduction in gas fuel costs.
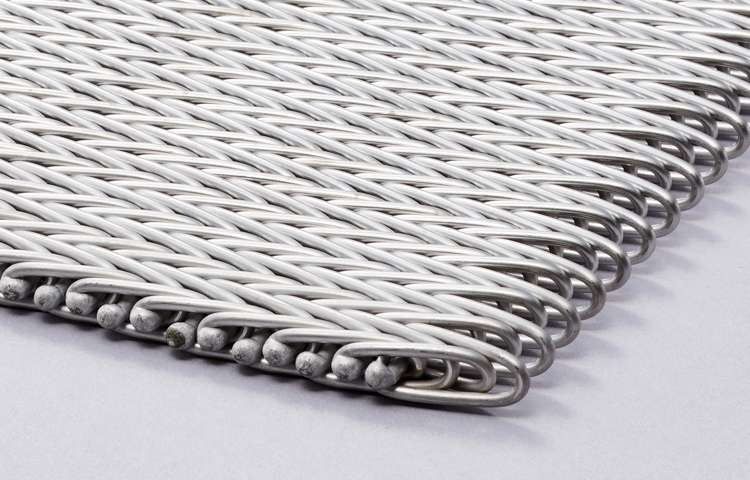
Customer Issue
Amount of gas used to raise the temperature inside the furnace
As the belt absorbs heat, it is difficult to raise the temperature inside the furnace, and a very large amount of fuel is used to raise the temperature to the specified temperature.
In particular, fuel costs tend to increase in the first few months after replacing belts with new ones.
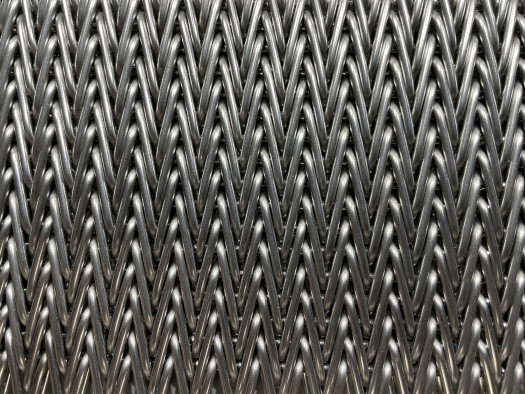
Our proposal
Review belt specifications to reduce weight
Consider whether reducing the weight of the belt decreases the amount of heat absorbed and cuts the fuel cost spent before heating.
Based on the structure of the conveyor itself and the shape and weight of the conveyor, the optimal belt material, mesh, and wire diameter are reviewed.
We judged that the foreign-made belt used was over engineered, and proposed a 25% reduction in weight.
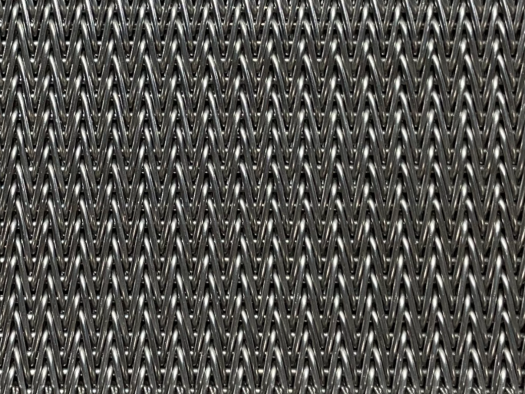
Effect after introduction
Reduction of gas fuel costs and belt purchase costs
By optimizing belt specifications and reducing weight by 25%, gas usage decreased immediately after replacing it with a new belt, leading to a reduction of 10-15% throughout the year.
At the same time, the weight of the belt reduced the amount of materials used, and the purchase cost was reduced by about 20%.
Products used this time
- Wire Conveyor Belt
- Chemical
- Automotive
- Electronic Parts
- Machine
- Metal Parts
- Heating
- Heat Treatment
- Conveying