
Technical Information
Wire conveyor belt and Conveyor Equipment
Overall mechanism and components
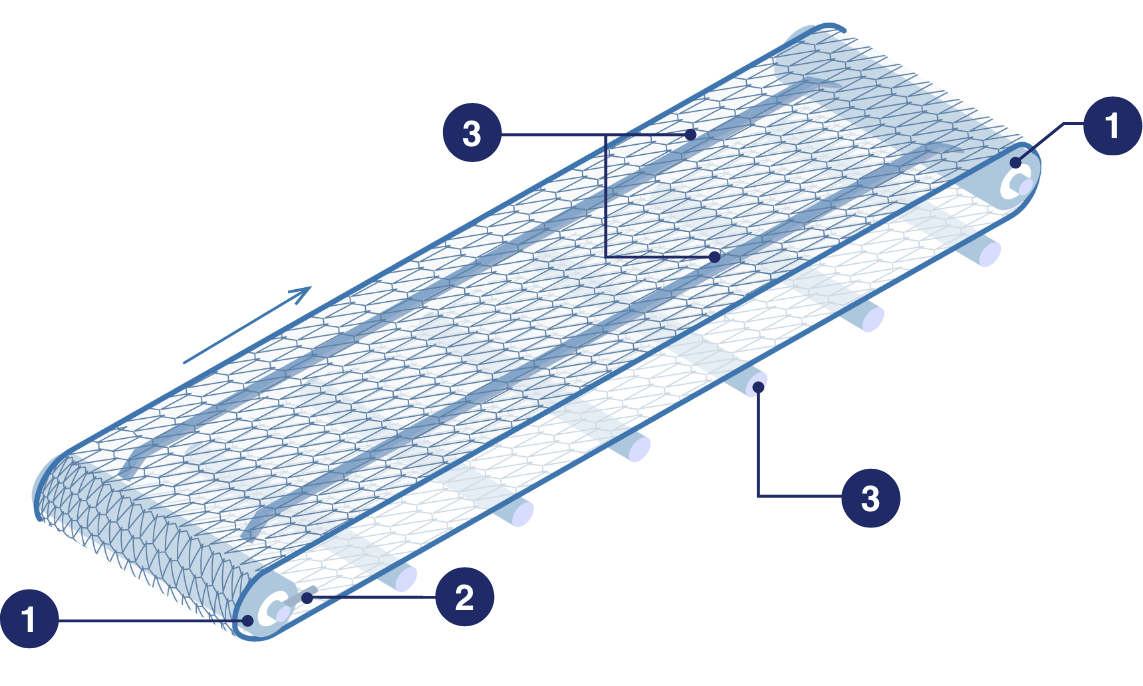
Above is an image diagram of wire conveyor belt installed on the conveyor equipment(the layout of the diagram is a simplified and there are other layout equipments).
The wire conveyor belt is called mesh belt, and the Conveyor device is also called the main body of Conveyor or the main body.
The main components of the conveyor system are
①Drive Unit and Service Unit 2 Take-up part 3 Belt Support Dept. Yes, there is.
Here we explain the relation ship between wire conveyor belt and these components.
①Drive Unit and Service Unit
Drive method
There are two methods of driving wire conveyor belt, sprocket drive and friction drive. Please refer to "Belt Type Selection Flow (Example)" for the main use of sprocket drive and friction drive.
Belt-type selection flow (example)Sprocket drive (direct drive)
This is a method in which parts such as belt meshes, chains (roller chains, conveyor chains), and pieces are driven by sprockets (gears, gears) by hanging the teeth of a sprocket. Since slipping and meandering are few, it is easy to run safely. The shape of sprocket differes depending on the type of belt. Direct drive belt (DDK2, FW, R1, BL...etc.) must be used with sprockets desinged to engage with mesh aperture. In addition, the standard specifications of the belt are determined to use a dedicated sprocket tailored to the mesh.
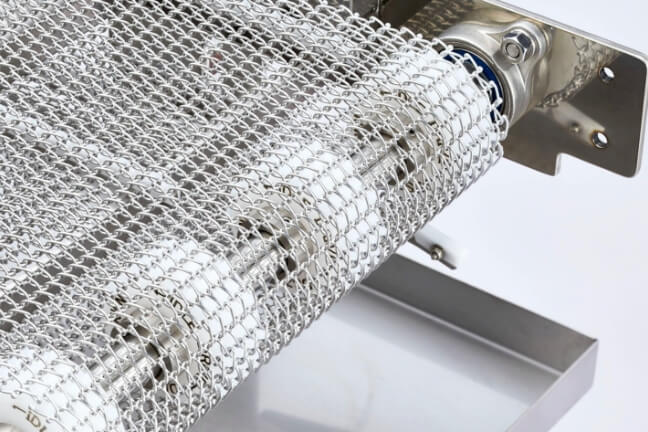
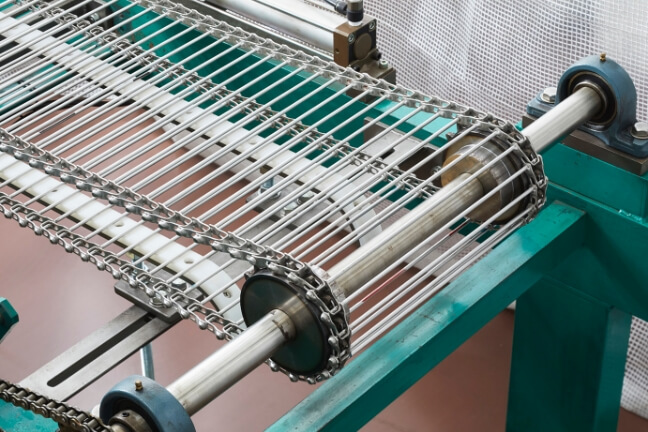
Drum drive (friction drive)
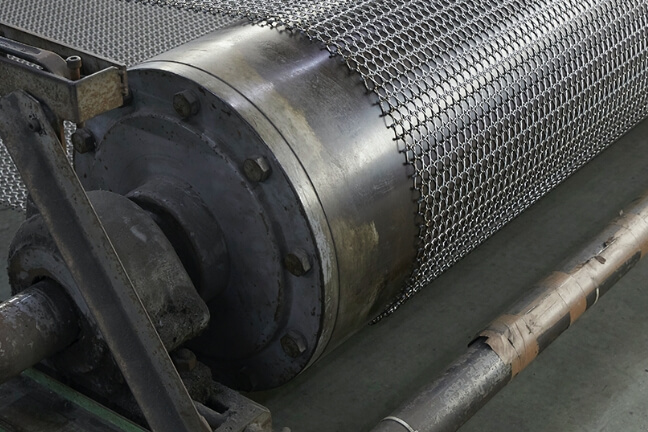
This is a method in which belt is contacted with surface of drive roller under tension and driven by frictional force between belt surface and drive roller. In order to increase friction, the drive roller may be coated with rubber or knurling is applied.
In general, tension given to the belt is larger than direct drive and the quipment is larger. Please refer to the catalog for how to drive the drum.
Roller diameter at the drive/idler unit
The drive/idler part is where the wire conveyor belt wraps around the roller or sprocket. Care should be taken when wrapping around the roller, as the belt may not run well depending on the roller diameter.
Rod pitch and roller diameter
Many wire conveyor belts can be wrapped around a fairly small radius roller, but if the roller diamter is not appropriate, the belt will not run well or the belt life will be shortened.
Roller Diameter and Net Flange Inner Height
There are considerable restriction on flexibility of belt with net flange. Care should be taken, especially if there is reverse radius in belt path.
Chain Plate Height and Reverse Radius
When using chain with flange plate, if there is revsese radius in belt path, you must be careful of interference between the flanges.
※In addition to the above, there is a factor that determines the roller diameter of the drive/indler unit, and please note that even our recommended diameter may cause the belt to slip depnding on the product weight and other conditions.
②Take Up Unit
Teke-up is a mechanism for applying appropriate tension to wire conveyor belt, and is also called a teke-up unit or tension device.
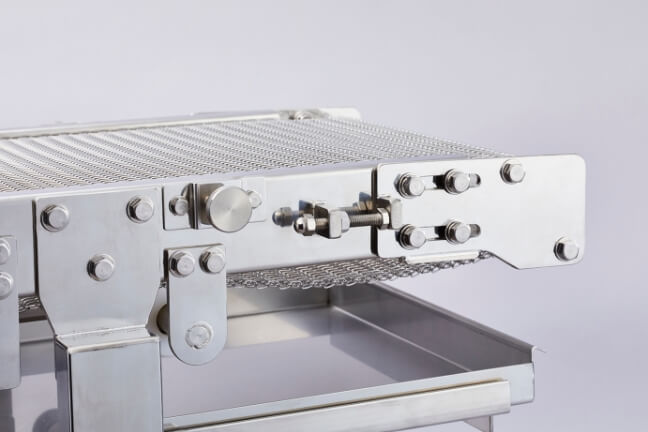
If the tension on the belt is not appropriate, it may cause trouble such as following
- Tooth jumping and riding on a sprocket drive
- Drive slip and meandering
- interference in belt support and other conveyor components
- Deformation of the axis
This may cause trouble.
In particular, the belt gradually stretches during use to reduce tension.
You need to adjust take-up regulary to keep the proper tension. The picture is an example of a screw-type teke up.
③Belt Support Unit
The part supports the belt between rollers such as drive and idler. Belt support is broadly divided into rail support and roller support.
Rail support

The rail support the belt. It is called a receiving rail, support rail, etc.
Generally plastic rails are used. In ordr to prevent the local wear of the belt, the arrangement of the support rails may be made into herringbone shape or lattice shape.
Roller support
The belt is supported by multiple rollers. It is called a roller or a support roller.
It is available to reduce the tension of the belt compared to the support of the rail. It is often used on the return path because the belt somewhat hangs down between rollers. The belt may vibrate, so it is not suitable when a severe alignment of the transport is required.